Quality Consulting Inc.
Services
WHY COMPANIES NEED A CONSULTANT
ISO does not permit registrars to perform consulting services which prepare their clients for the certification audit. This prevents conflicts of interest. Since the standards were written to be broadly applicable, most organizations require some outside help to understand how to conform in practical, auditable terms.
We recommend starting with a small amount of guidance to help you understand the scope of what will be required in terms of resources, time and cost. Then you will be able to determine how much or how little outside help you require. In general, the more you can do internally the more beneficial toe exercise will be, but this is not always the case.
Some common standards QCI consults for
ISO 9001: Quality Management Systems
IATF 16949: 2016 Automotive Quality Management System Standards
ISO 14001: 2015 Environmental Management Systems
ISO 45001: 2018 Occupational Health and Safety Management Systems
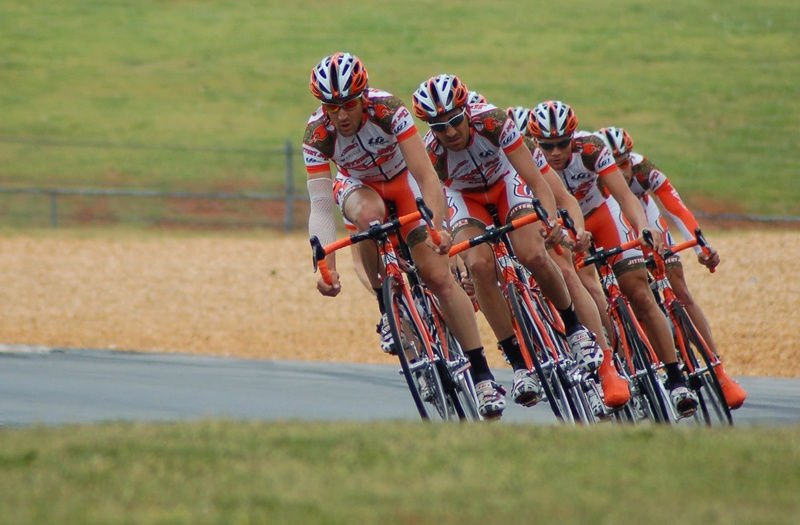
I'm a paragraph. Click here to add your own text and edit me.
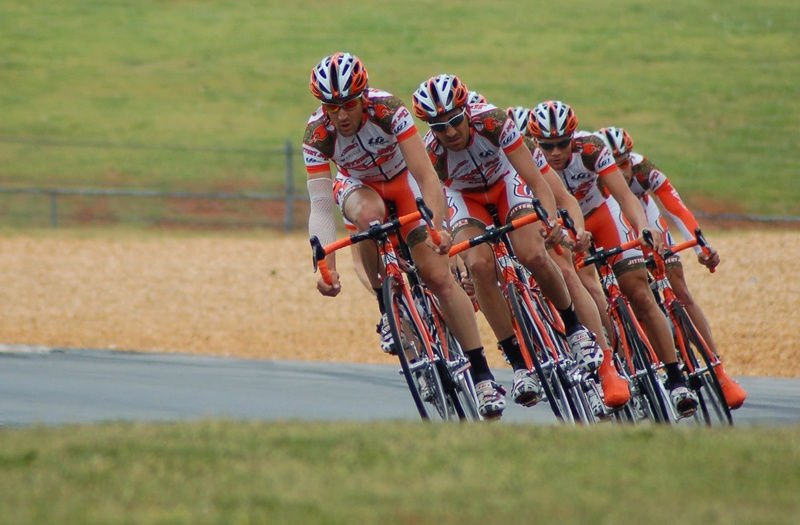
I'm a paragraph. Click here to add your own text and edit me.
CONSULTING AND TRAINING THAT FITS YOUR NEEDS
Top Management Orientation
The standards were revised to emphasize the importance of leadership. Our consultants work with top management to understand their roles, establish objectives, set policy, oversee communication and manage resources.
Gap Analysis
How does your management system stack up against the requirements of the standards? Are you ready for a registration, transition or renewal audit? Our expert consultants pinpoint where you are and what you need to do to get over the finish line.
Internal Audits
Outsourcing your internal audits is not only efficient but more effective, yielding better results. Our trained and certified consultants understand what the registrars are looking for. Get more than just an audit, get advice. Since QCI does not provide certification audits we can do more than just audit, Our experts have each done hundreds of audits. We can show you simple, common solutions to a variety of system problems.
Supplier Audits
Organizations must audit their suppliers frequently to ensure the suppliers' internal processes adhere to a defined quality standard. We provide the resources to evaluate your suppliers efficiently. This is crucial for all of the quality system standards. QCI has vast understanding of many business areas, including automotive, education and government.
Training
Courses can be tailored to your organization. Course offerings include:
Overview
Internal auditors
Lead auditors
Implementers
Corrective Action Follow-up
One of the biggest problems is effectively closing out your corrective actions from audits and customer complaints. One of the steps in 8D is implement and validate permanent corrective action. Another step is prevent recurrence. The inability to do either of these is a common cause of corrective actions being rejected by registrars. This service offers techniques for ensuring effective corrective actions have been implemented.
Problem Solving and Root Cause Analysis
* How to identify a problem that is best solved by the 8D approach
* How to write a problem statement that has just one problem
* How to create an effective team
* When do you need a team
* Learn about team and group dynamics
* How to develop interim containment solutions to protect the customer
* How to us popular quality tools to find root cause
* How to find the single root cause
* How to know when you have found the true root cause
* What is an escape point and how to find it
* How to analyze possible permanent corrective actions for effectiveness
* How to apply a permanent corrective action
* How to prevent recurrence
* How to make this eight discipline problem solving method work as a structured, disciplined system in your business
Risk Analysis (pFMEA, SWOT)
Core Tools / Automotive Industry
For those organizations in the Automotive world you understand that registrars seek evidence that employees have had expert training in SPC, MSA, APQP, FMEA and PPAP. Our consultants/trainers provide that expertise and will guide you through each of the core tools and they also integrate the core tools with each other. Further emphasis on where core tools are applied in the IATF 16949 standard and customer specific requirements.